
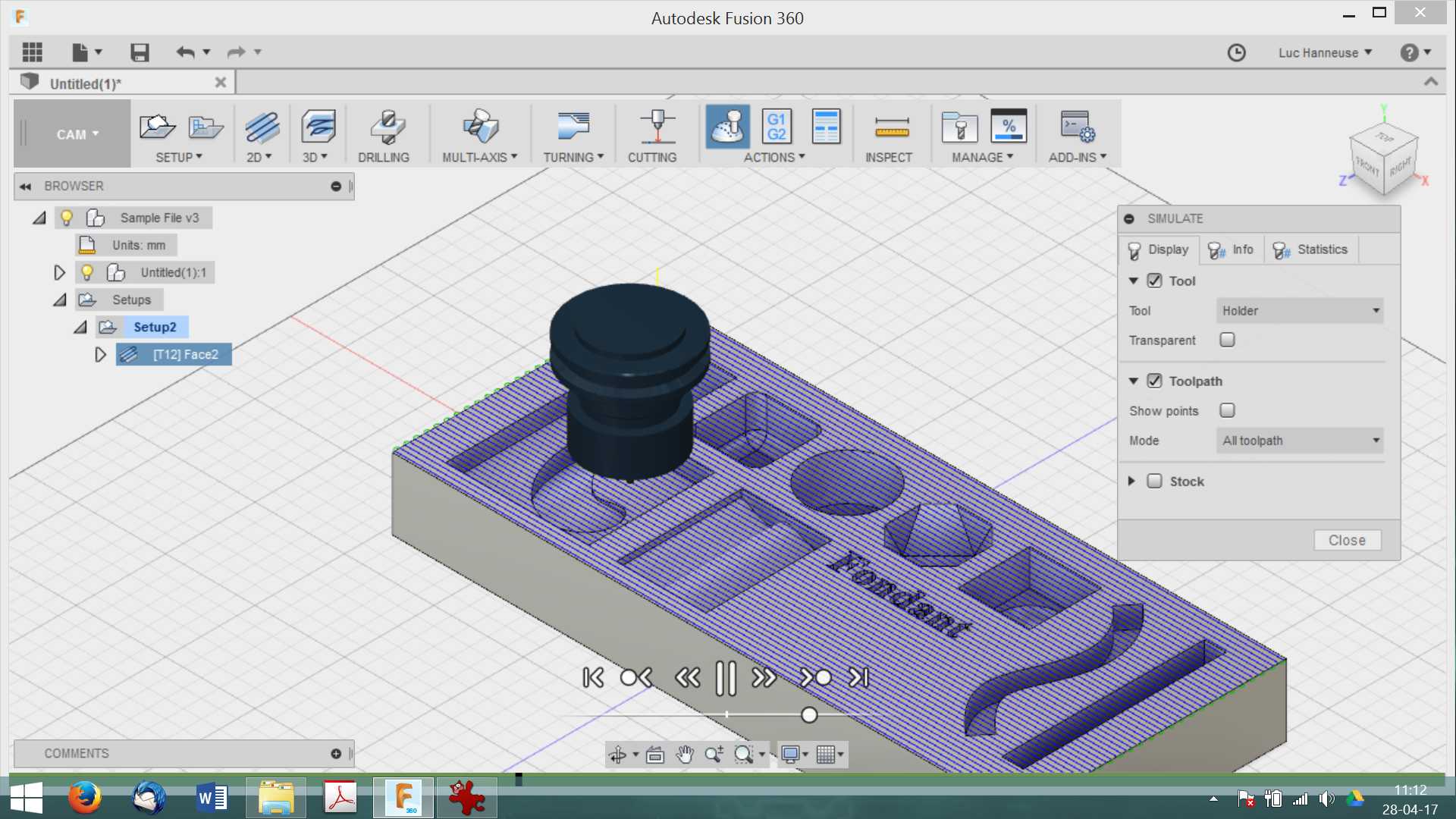
I use this macro to set the offset in X, Y, and Z. I have a laser attached next to the spindle (magnetically removable optlaser). This sets the location of my machine X0 Y0 work coordinates Then stores the difference between the probe and the waste board. 02 and 04 need to be changed when resurfacing the waste boardįirst sets the location of the probe and permanently stores this infoĠ2 - Set Probe to Waste Board Distance G55

macros 01-04 are for initial setup of the machine. I'll provide a workflow here as well as I think it's helpful.Īgain, my machine has a fixed z probe button just off the work area. If you want to run a different macro, simply open up the post processor in Visual Studio Code and change the file path at LINE 573, save, and reupload to F360.įor the macros, these were written mostly by for his moot line of CNC machines. It does this by calling on macros I have also provided here.

The post processor will call for a tool change if required. Upload the post processor I have provided. M42 P1 S0 Ensure P1 is off - enable input #1 M950 P1 C"io4.out" Use C"" for output - Opt Lasers enable input #1 Create enough tools to cover library of F360 CAM tools and link to R0 M563 P2 S"Spindle" R0 Create tool 2 with Spindle M950 R0 C"out0+out6" Q300 L0:24000 Select Spindle On/Off,RPM & Direction (not selected). In my config.g file, I have as many Tx as I have bits in my library. Save to the cloud tool library (preferences -> manufacture -> enable cloud libraries). Note: a new tool will default to the lowest available number so make sure you add it to the bottom of the list. Use T3 and above in Fusion 360 for defining bits. Using T0 has caused me issues, so I avoid using that. I reserve T1-T2 for defining tools such as spindles and laser engravers in my config files. I've also enabled arcs in this post processor.įirst setup your tool library in Fusion 360 including data on spindle speeds and feedrates. I'll cover how I build a tool library in Fusion 360 and call macros for a manual tool change between operations with a modified post processor for a pwm controlled spindle and a stationary z probe. I'm running RRFW 3.3 on a Duet 3 running 32v for motors and 24v for most everything else. I thought I'd provide a workflow for those interested in using Fusion 360 for CNC and laser work.
